Can Custom Tooling Save Time and Money? YES!
Did you know that custom tooling has the potential to save you time and money?
Most people associate custom tooling with increased costs and lead times, but here at our precision machine shop, we think custom tooling doesn’t always deserve its negative reputation.
While it isn’t the best solution for a single component or prototype model, custom tooling can make sound financial sense for production manufacturing.
The Benefits of Custom Tooling
1. Saves time and money on high-volume jobs
There are, of course, upfront costs associated with making custom tooling, but a one-time investment yields long-term savings if the production volume is high enough. And the savings keep growing for repeat production orders.
Once we’ve designed a custom tool, we can use that design for every order you place with us. What’s more, if you design multiple parts with the same geometries (which often happens in assembly design), we can use the same tooling across those different parts.
2. Cuts multiple profiles simultaneously
We can design and order a single tool ground with a specific profile to cut multiple features simultaneously, yielding significant time (and cost) savings.
For example, if a part has a top and bottom radius and a vertical wall, a custom tool could be used to achieve those features simultaneously. The alternative precision machining solution would involve multiple tools and setups. We’ve seen cycle times of 10 minutes per part decrease to just one minute per part with custom tooling.
3. Machines complex parts in 1-2 passes
Custom tooling is incredibly useful for complex parts, enabling us to use a single tool and a single pass to achieve intricate surfaces.
With custom tooling, it’s possible to cut features like counterbores and through-holes with incredible speed and precision. Let’s say the counterbores have radii at the bottom and a through-hole with a more precise diameter for something like a shoulder screw. One single cut using the custom tooling could achieve both the bottom dimension and the tight tolerance. Our team could drill, pilot, and plunge once to make the part.
How KAD Approaches Custom Tooling
While we’re known for our expert prototype machining services here at KAD, we’re always finding ways to innovate at the production level, too. We love working with customers on their production manufacturing projects.
We may recommend a specialty tool for higher production parts to reduce costs. We determine the need for custom tooling, design it for the customer, and have it made by a highly-skilled custom tooling supplier.
Customers can expect a non-recurring engineering (NRE) fee for the tooling, but we also provide a breakdown that explains how the tooling will create savings in the long run.
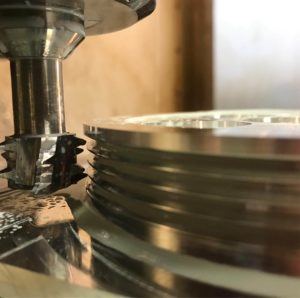
Tooling in Action: A Pulley
We recently made custom tooling for this aluminum pulley. The tool we developed for it looks like a mace, and the entire profile of the pulley is ground onto its surface.
Now that we have this tool, we can make pulleys with different numbers of grooves, so the customer gets to iterate on the number of grooves in their design without purchasing new tooling. We can do the entire part in two passes: one rough and one finish. The alternative approach—turning the part on a lathe—would be a much more time-consuming process.
Are you ready to tackle a production manufacturing order and curious about custom tooling? The KAD team would love to partner with you on your latest project, whether big or small. Simply request a quote to get started.